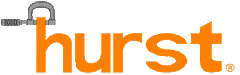
Voltage: | 12-45Vdc for Analog and PWM Control Methods 12-48 Vdc with Hall Output |
Operating Modes: | External, Open Loop Speed, Closed Loop Speed, Torque (Open Loop), Preset Speed |
Control Methods: | Analog, PWM, PWM & Direction Note: These control methods are available with or without an internally supplied 5Vdc power supply. |
Encoder Options: | 100, 250, 256 w/ index, 400, 1000 line available |
Protection: | Current Limit Under Voltage |
Integral Design: | Fits on the back of our HST23 and Dynamo Brushless DC motors |
Motor Power Supply Connections: | |||
![]() | |||
Pin Number | Description | Input/Output | Notes |
1 | +DC | Input |
12-45Vdc for Analog and PWM Control Methods 12-48 Vdc with Hall Output (Feedback Board Only) |
2 | GND | Input | |
Control Connections: |
|||
![]() |
|||
Pin Number | Description | Input/Output | Notes |
1 | Tachometer | Output |
Speed Output – 15 Pulses/Revolution (PPR) for Dynamo and 9
PPR for HST23 at TTL Level (0 to 5 Vdc) and 50% Duty Cycle |
2 | Speed/Torque | Input | Only used for Analog Control Method |
3 | PWM | Input |
0% duty cycle minimum command 100% duty cycle maximum command Used with Direction Input pin (Pin 7) |
4 | Encoder Channel B | Output | Speed and Direction Output – PPR based on encoder line count at TTL Level (0 to 5 Vdc) and 50% Duty Cycle; No output if encoder not present |
5 | Encoder Channel A | Output | Speed and Direction Output – PPR based on encoder line count at TTL Level (0 to 5 Vdc) and 50% Duty Cycle; No output if encoder not present |
6 | Direction | Output |
0 Vdc
output = clockwise lead end 5 Vdc output = counter-clockwise lead end Can be used in conjunction with Tachometer output (Pin 1) to determine speed and direction |
7 |
Direction / PWM & Direction |
Input |
Direction - Used in conjunction with PWM (Pin 3) and Speed/Torque (Pin 2) PWM & Direction - |
8 | Enable | Input | Low Level signal (0 Vdc) enables drive |
9 | GND | -- | Return path for +5 VDc (Pin 10) |
10 | +5 Vdc | Input / Output |
Input - User supplied 5Vdc Output - Optional Integral 5Vdc supply |
|